The True Cost of Petroleum Oil Tank Replacement
How Facilities Can Save Time and Money on Tank Replacements
A CASE STUDY
Petroleum storage tanks have an expiration date in terms of warranty and age. Their lifespan is only so long. But many healthcare facilities keep their tanks operational without any plans to replace them.
Although healthcare facilities are seldom proactive when it comes to replacing their tanks, it can save thousands of dollars in the long run. That’s what a Northern Alabama hospital found out. They saved $43,000-$50,000 and six weeks of project time by planning a proactive tank replacement.
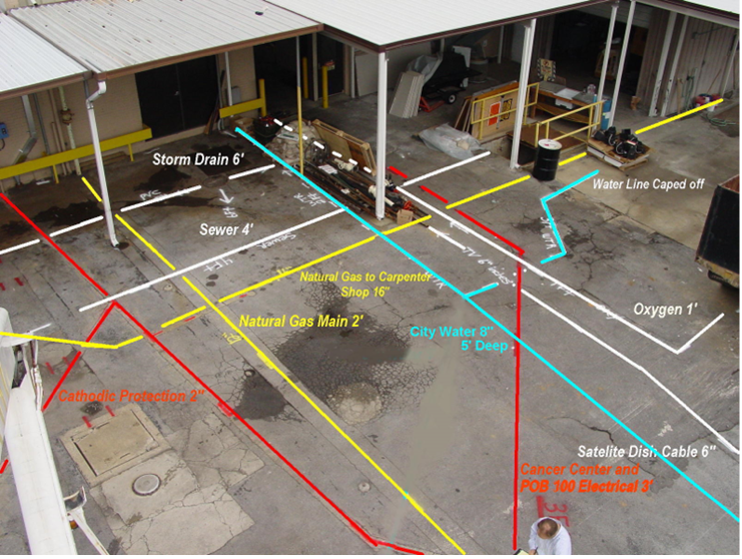
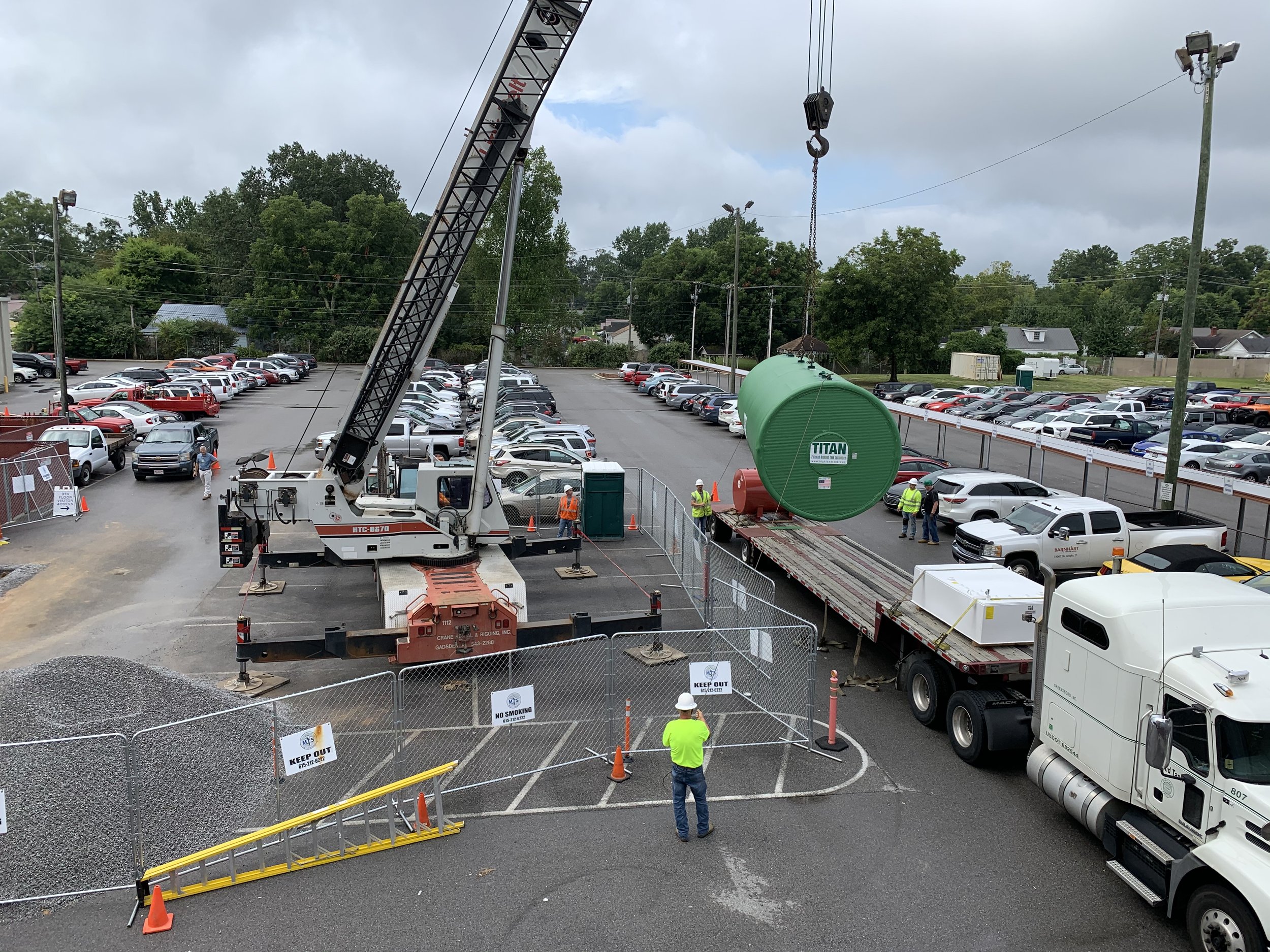
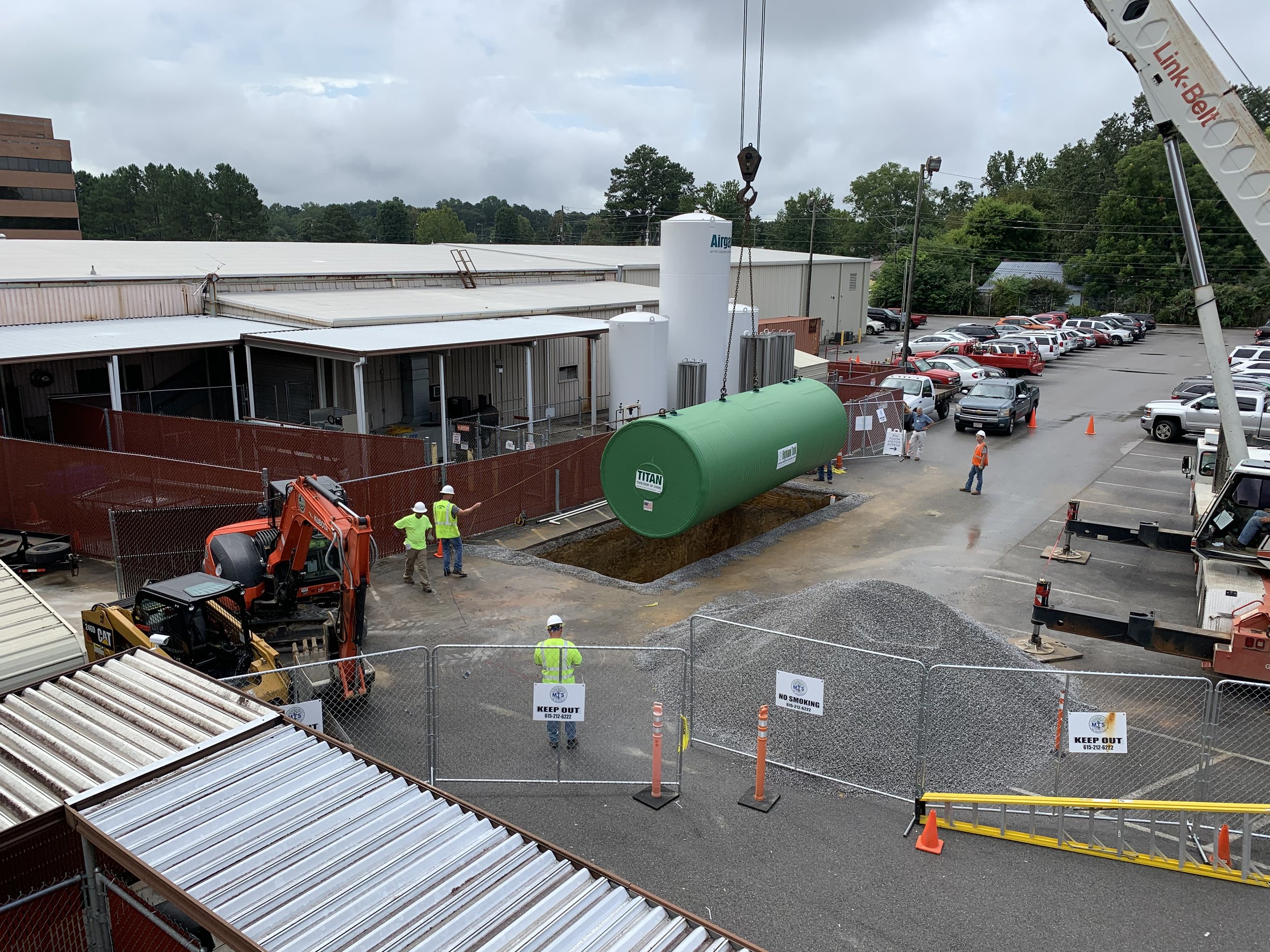

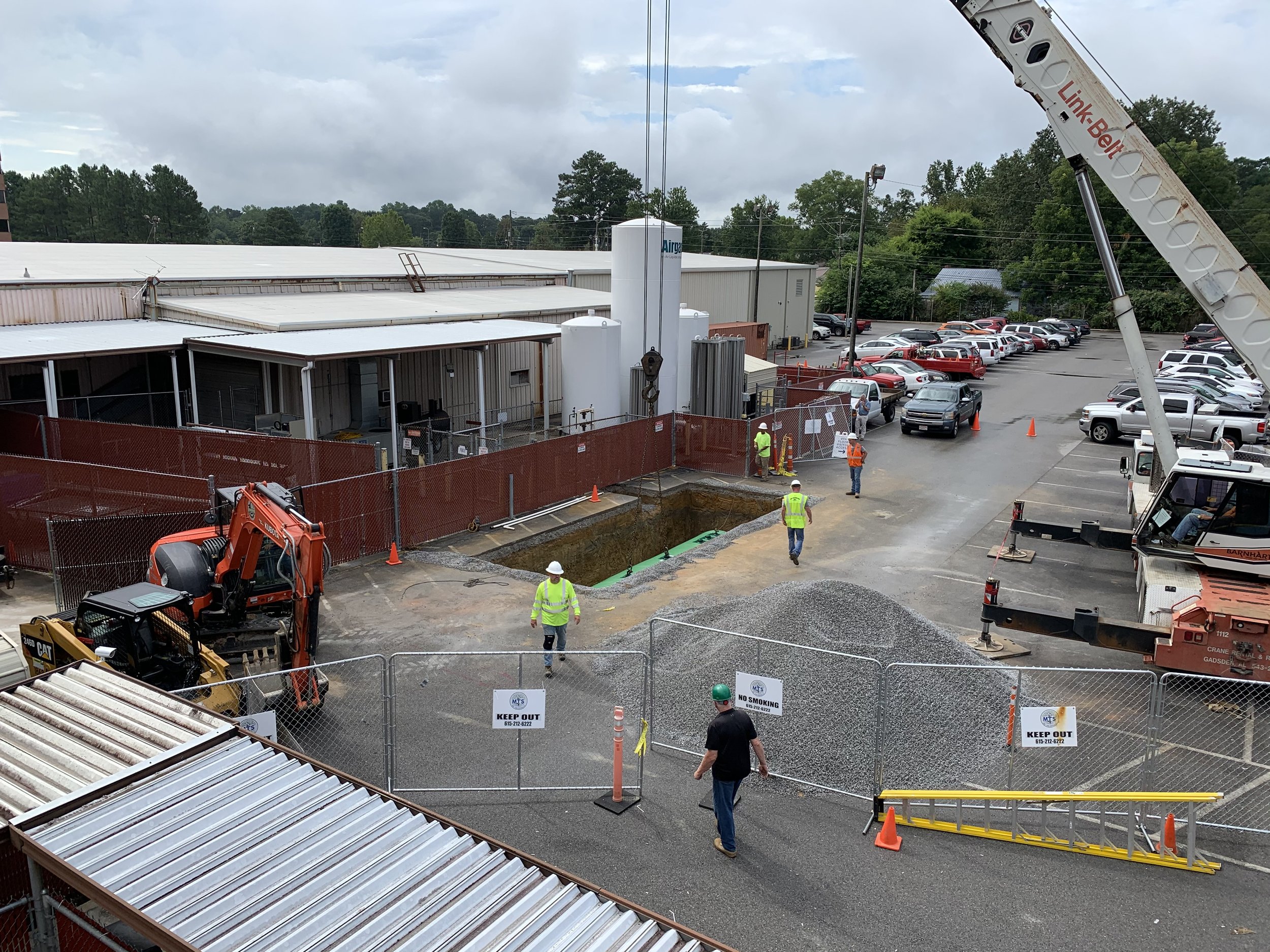
Project Highlights
Construction Timeline:
February - September 2020
Budget:
$216,000
Project Scope:
Install a new double-wall, poly-jacketed, 10,000-gallon underground storage tank (UST)
Close the 40-year-old UST
Streamline the efficiency of the new system by eliminating cathodic protection on the UST
Project Outcomes:
Provided a more accessible petroleum storage tank for scheduled fuel deliveries
Put in a modern system with improved leak detection and potential preventative fuel loss control measures
Closed-in-place the old tank within a very complicated array of subsurface utilities
Client
A National Healthcare client with a hospital located in the Northern Alabama region. The Joint Commission-accredited facility offers inpatient and outpatient care in cardiology, pulmonology, sleep medicine, and stroke services.
Challenges and Objectives
By planning for the new storage tank, the hospital managed to avoid expensive issues that we see other facilities face.
Another GHP client experienced an unexpected and costly dilemma in 2021 when two of their three aging petroleum storage tanks failed. These tanks, two 20,000-gallon ones and another that was 12,000 gallons, were past their 30-year warranty. Replacing these tanks with new tanks cost the hospital over $1 million and took 17 months to complete. Had the facility planned for the inevitable replacement of these older tanks, they could have significantly reduced the costs and project timeline.
The sudden failure also created scheduling difficulties. Obtaining replacements for the tank systems would take 22 weeks. Budgeting was not prepared, causing project expenses to skyrocket. Immediate solutions such as temporary fuel storage cost $40,000 for an entire year. The facility needed to establish a new backup fuel source as quickly as possible so it had few options for more strategic replacement solutions.
Fortunately, this project didn’t have contamination from the tank failure. Had there been a fuel loss, they would have had to handle federal, state, and local regulators, mount a remediation effort to clean up the spill, and face liability for large penalties. This could have caused costs to inflate another $500,000 in addition to the tank replacement costs.
From this project and others we see, the common risks of an emergency tank replacement include:
Schedule for replacement becomes inflexible and can cause significant interruptions to facility operations
Immediate and expensive action needed for stabilization of failed tanks
Unexpected expenditure for temporary fuel storage before new tanks are functional
Extensive lead times for new tanks that were not previously accounted for
Immediate solutions without time for thorough assessments that cater to future expansions
Solution
The hospital didn’t experience any of these risks. It took the initiative to proactively replace its 40-year-old, 10,000-gallon tank with a modern equivalent before costly failures emerged. GHP assessed the tank, determined the best time for replacement, and set a budget for the project.
If the client hadn’t chosen to replace its UST, it would have eventually become a necessity. Our pre-construction audit showed an ongoing compliance issue that would have resulted in forced UST closure/upgrade by regulatory authorities.
Proactivity allowed for ample time to assess, strategize, and identify a sustainable location for a new UST. GHP reviewed above-ground storage tank options for the facility. However, due to higher costs and spatial limitations of the facility, a UST replacement was the most fitting option. In addition, the existing UST was heavily surrounded by infrastructure so it required closure-in-place, the filling of the old UST in order to take it out of service.
Along with preplanning the location for the tank replacement, the hospital managed its own replacement schedule to make sure it did not affect normal operations. The planning and bidding of the operation happened concurrently with the onset of COVID-19, resulting in a cost reduction and a shortened lead time compared to the current supply chain challenges in the tank industry.
Results
With an established plan for its tank replacement, the client replaced their UST without facing any unforeseen challenges. The result was a swift replacement within a mere 7 months at a total project cost that stayed within the set budget. The timing of the tank order led to a cost savings of 20% and a significantly shortened lead time. The new UST is also more efficient. The hospital cut facility personnel time for monitoring fuel levels and overall compliance.
GHP’s initial assessments of the tanks lead to well-planned solutions, positioning the facility for the future.
Conclusion
This client and project exemplifies an effective strategy to mitigate the risks of emergency tank replacement. Facilities with aging tanks need to adopt a proactive approach for replacing their aging petroleum storage tanks so they can ensure operational consistency, cost-effectiveness, and environmental safety.
Taking initiatives like these might seem burdensome upfront, but in the long run, they save time, money, and reputational damage. Instead of facing potential environmental disasters and unexpected costs, this hospital proved the benefits of forward-thinking planning.